Powering progress, from Namibia to the world
We power nuclear energy responsibly while fuelling careers, communities, and sustainable progress.
Powering progress, from Namibia to the world
Powering progress, from Namibia to the world
We power nuclear energy responsibly while fuelling careers, communities, and sustainable progress.
At Rössing Uranium, “U” is more than just a symbol – it represents you, the people we work with and for.
As one of the world’s largest operating open-pit uranium mines, we provide the global nuclear industry with responsibly mined uranium. But our commitment goes beyond production, it's about people.
We fuel careers, empower communities, and drive sustainable progress.
The Rössing mine, located in Namibia’s Erongo region, prioritises safety, sustainability, and innovation. Every step of our operation aligns with global best practices, ensuring responsible uranium production for a sustainable future in nuclear energy.
From the Namib desert to the world
Our purpose is to be a safe, responsible, and efficient Namibian producer and supplier of uranium to the global nuclear industry, creating optimal returns for shareholders and sustainable benefits to stakeholders.
SAFETY
We take care
RESPONSIBILITY
We create maximum value
INNOVATION
We seek excellence
COORDINATION
We achieve together
Operations
Our mining methods focus on efficiency and sustainability.
Using advanced open-pit techniques, we ensure responsible extraction while maintaining strict health and safety standards.
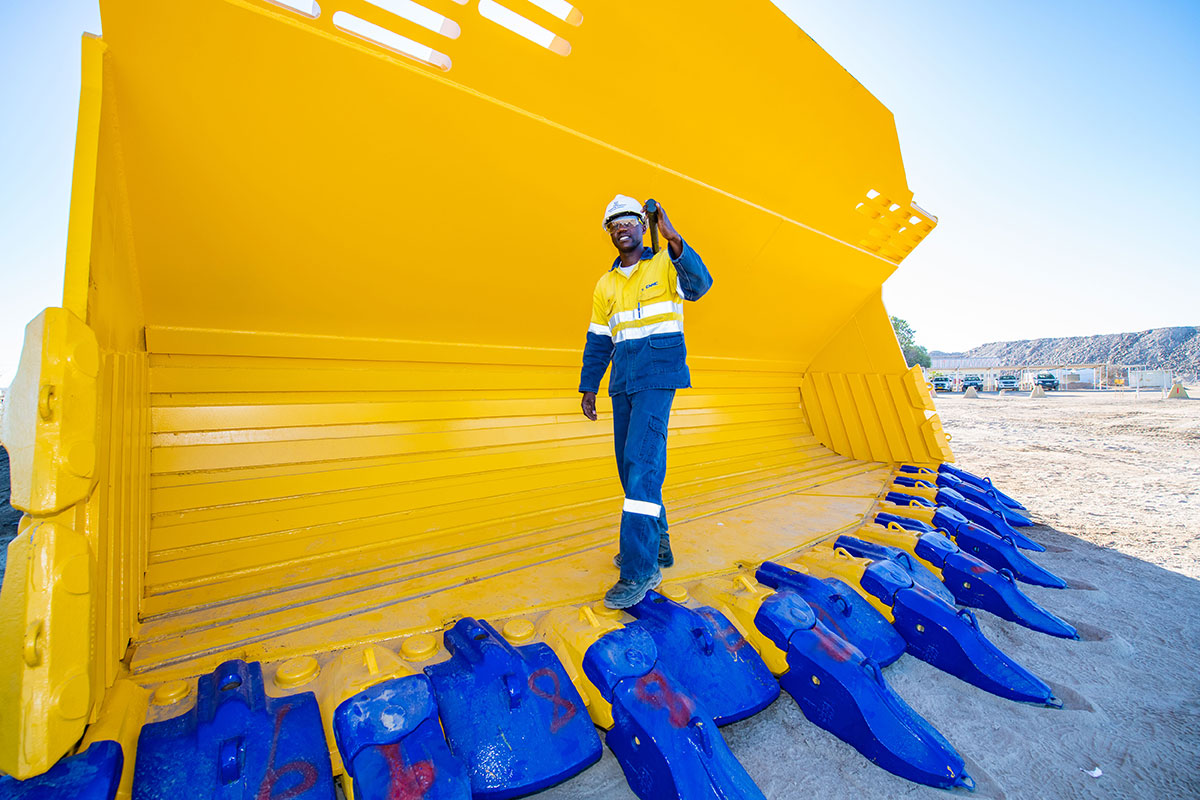
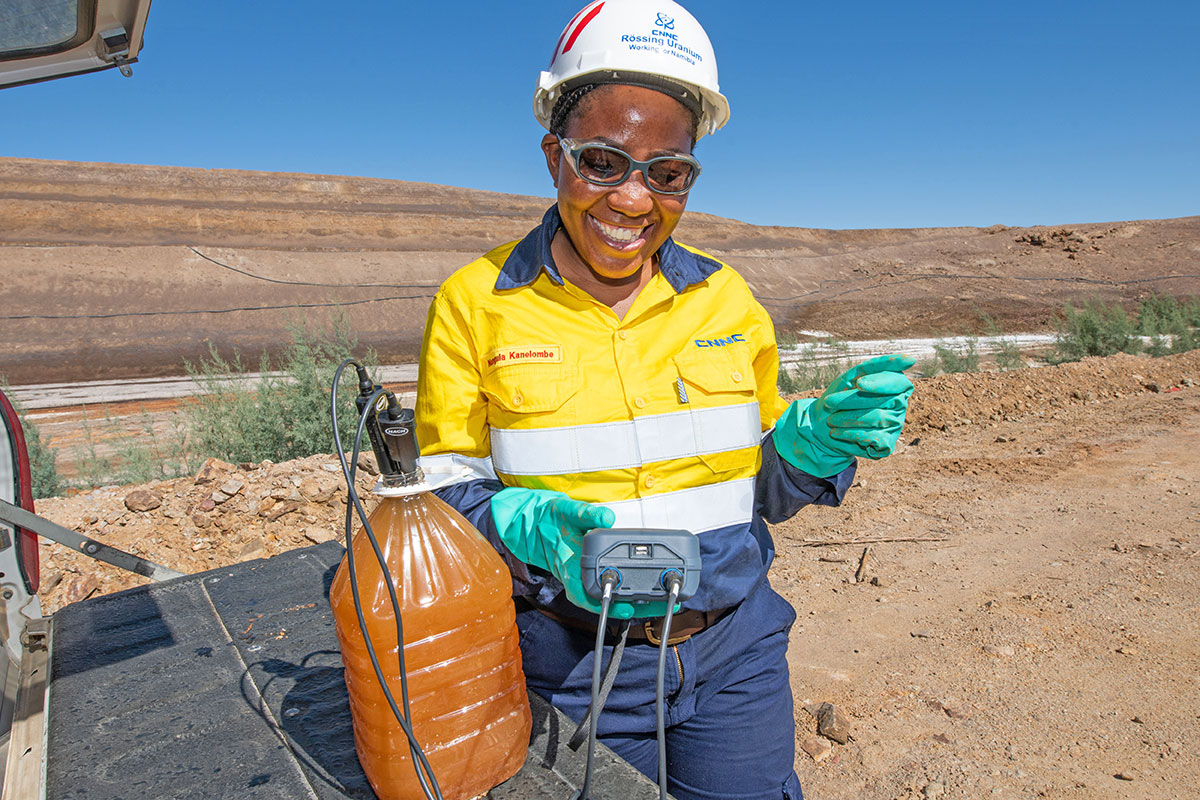
Sustainability
Sustainable development guides everything we do.
We actively minimise our environmental impact through water conservation, air-quality control, and responsible resource management. Our commitment extends beyond the mine, supporting local communities through education and healthcare initiatives.
Latest News
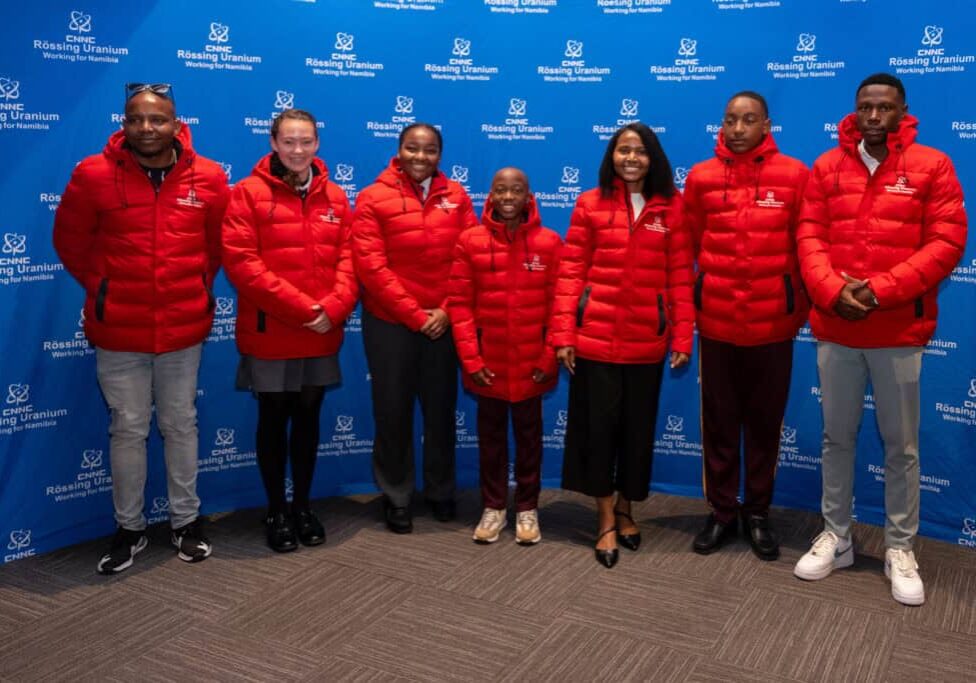
Rössing Uranium Invests in Youth Empowerment
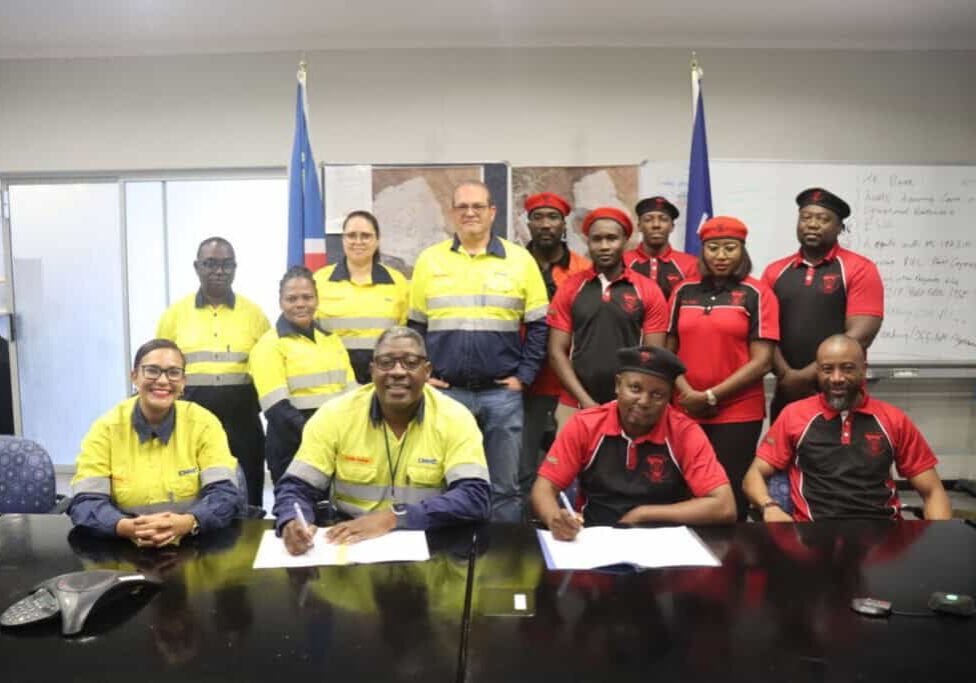